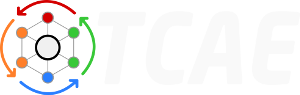
Manifold CFD Simulation
This case study shows a complex CFD and FEA analysis of exhaust manifold using simulation environment TCAE
FEA Simulation Report
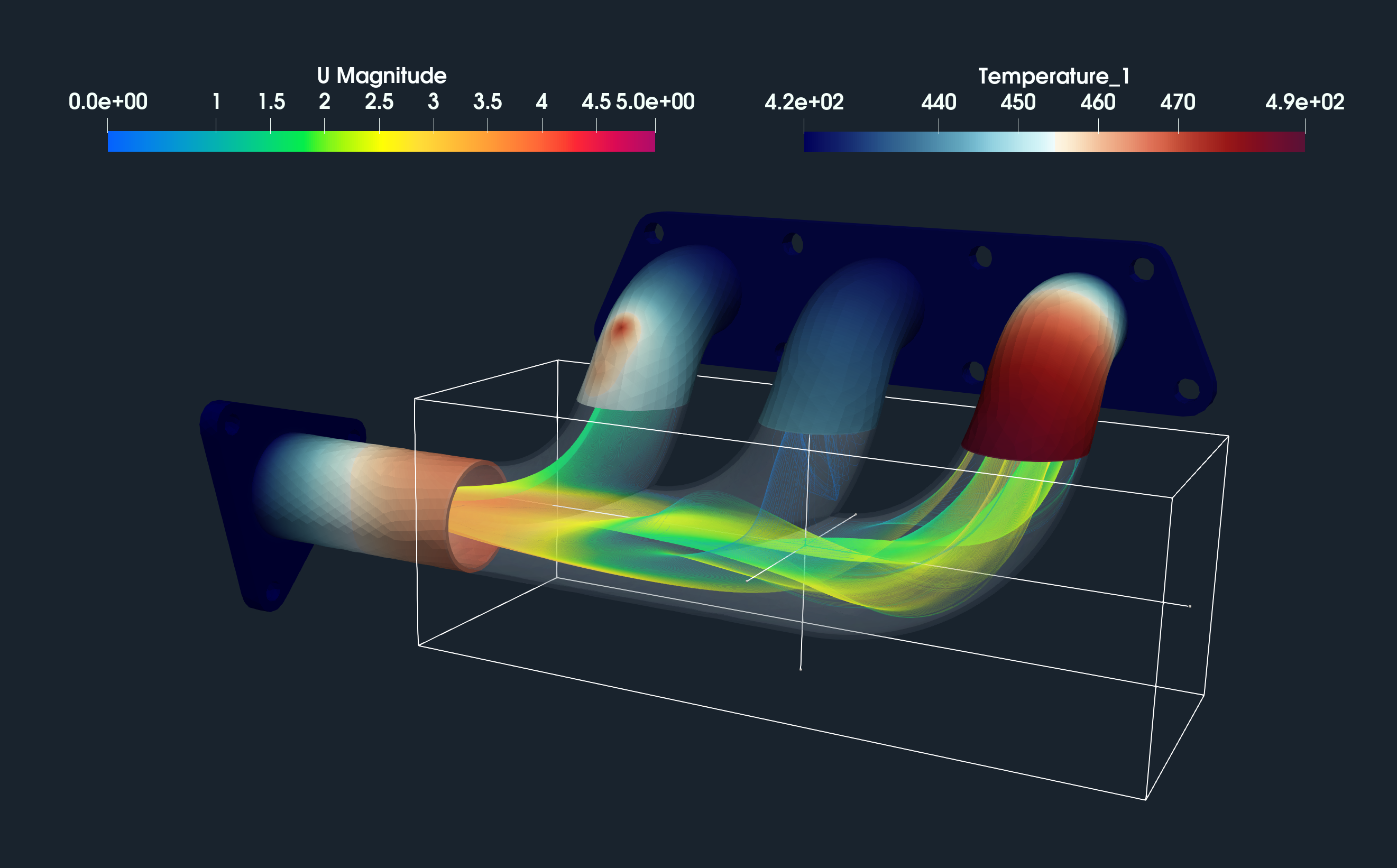
TCFD is automated workflow
CFD SUPPORT introduces the new generation of CFD simulations. TCFD brings an extreme increase of productivity to CFD simulations. TCFD is extremely popular project, because it successfully merged benefits of an open-source (perpetual, unlimited users, jobs, and cores, customizable, …) with benefits of commercial codes (professional support, well tested, ready for the industry, robust, accurate, automated, GUI, …).
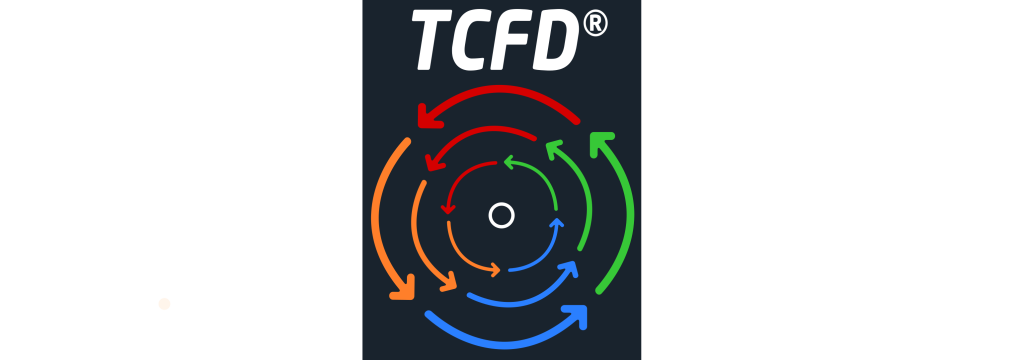
TCFD is fully automated, it can run the whole workflow by a single command: data input, new case is written down, mesh is created, case is set-up, case is simulated, results are evaluated and the results report is written down. Both GUI and batch mode. Data in – data out. TCFD is mainly focused on supporting the engineers in their real value added work. TCFD is fully automated and the beauty of TCFD is that it is the user who decides how deep to dive into a CFD or not at all. And all the options remain open at the same time.
Input data
The surface model data in .stl file format together with physical inputs are loaded in TCFD. Other option would be loading an external mesh in OpenFOAM® mesh format, or loading an MSH mesh format (Fluent mesh format). This CFD methodology employs a multi component approach, which means the model is split into a certain number of regions. In TCFD each region can have its own mesh and individual meshes comunicate via interfaces.
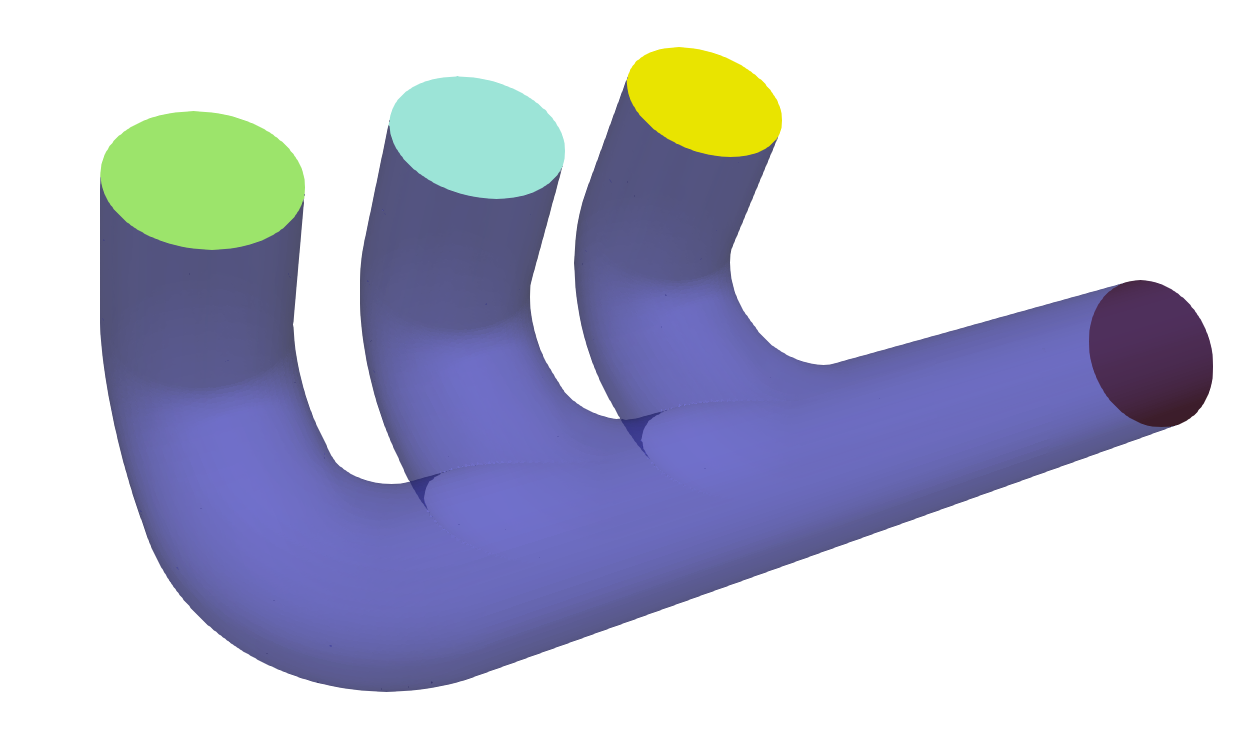
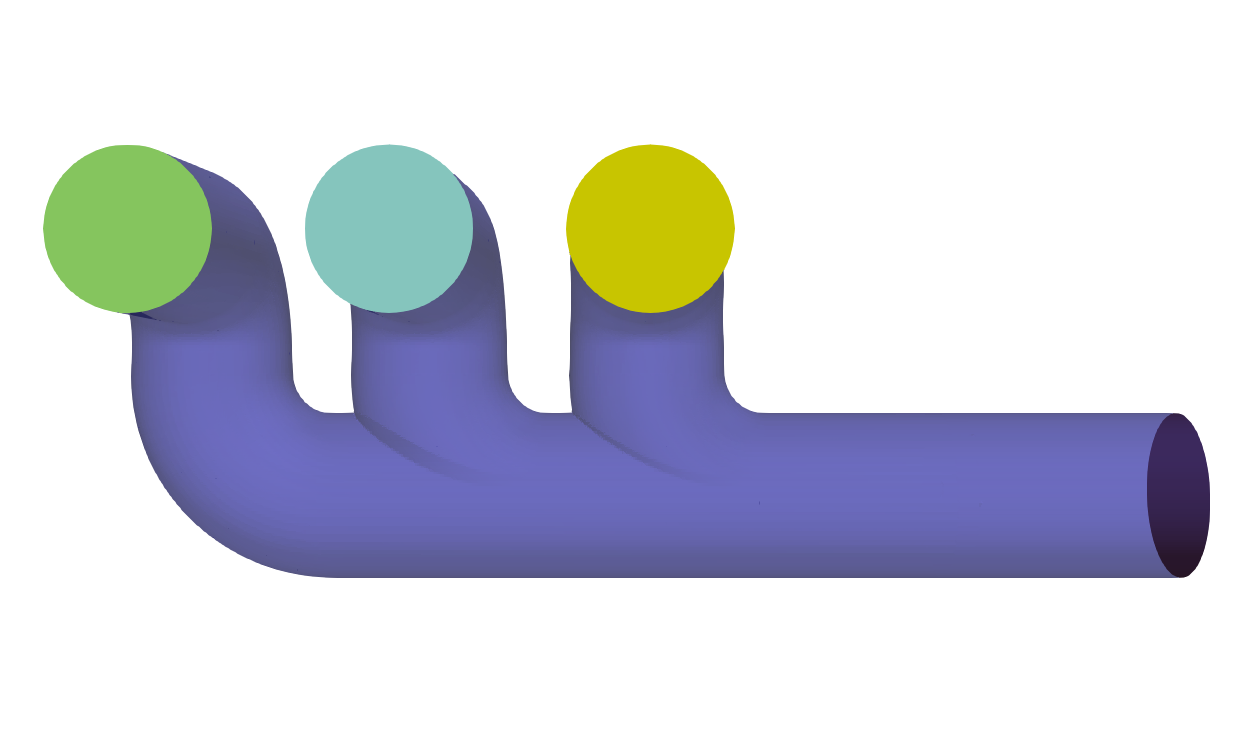
Easy to test the mesh sensitivity
In practise the rough mesh with no boundary layer (CPU time: 4 core*hours/single point) can give the same results as the fine mesh with boundary layer (CPU time: 20 core*hour/point). So finally, the rough mesh effect can eliminate the lack of boudary layer. Anyway, with fully automated workflow it is easy to make many tests to callibrate to actual machine data.
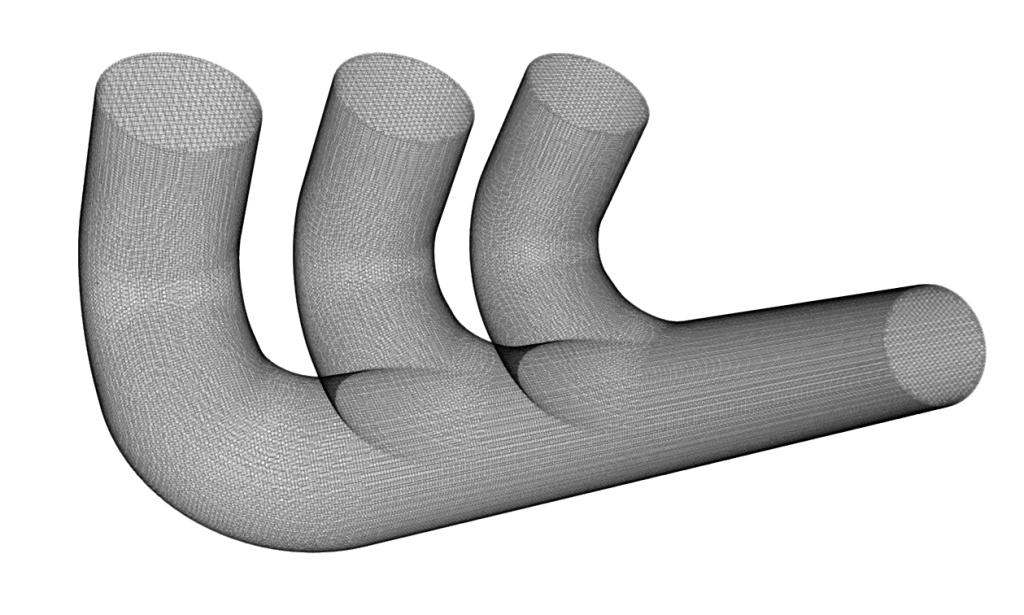
The component graph
Any project simulated in TCFD has its component graph. The component graph shows how the components are organized – the model topology. What is the inlet, the outlet and how the components are connected via interfaces.
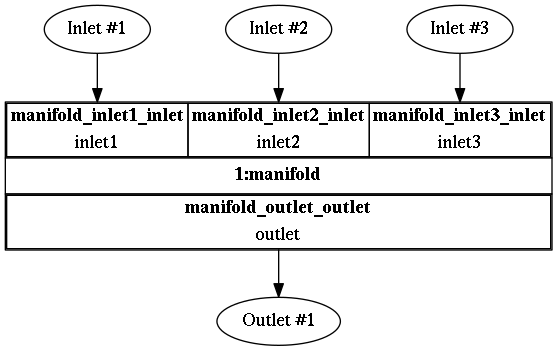
CFD Simulation Set-up
- Compressible flow model
- Transient flow model
- Medium: Hot air
- Temperature at inlet: T = 543 [K]
- Viscosity: μ = 1.831e-5 [Pa.s]
- Mass Flow Rate: 0.00468 [kg/s]
- Interface: None
- Turbulence Model: k-ω SST
- Mesh: snappyHexMesh, hexadominant
- Mesh Cells: 345250
- Number of components: 1 [-]
- CPU time: 3 [core.hours]
For more details of CFD Simulation Set-up see TCFD Manual.
Running CFD Simulation
The simulation can be run on any number of parallel processors. Immediately after the simulation is started, the user can follow the progress of all the important quantities in a HTML report: flow rates, residuals, efficiency, torque, pressure difference and many others. These run-time functions give the user valuable information of the simulation convergence and also the availability to stop the simulation before its expected end.
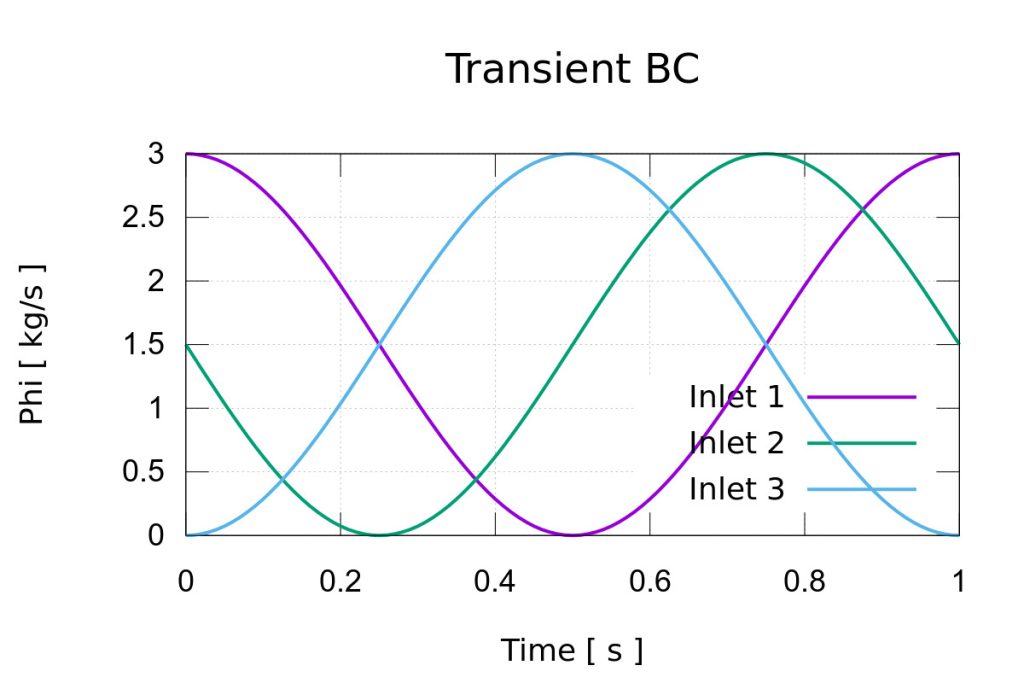
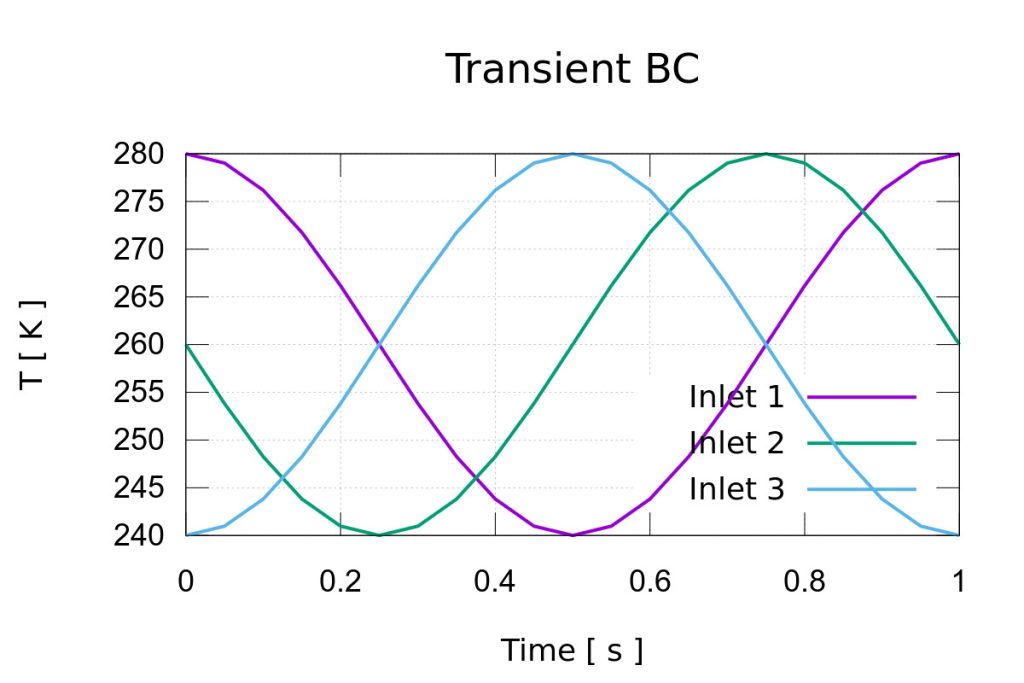
This manifold tutorial is special because of transient boundary conditions at the inlet. Mass flow rate and temperature change periodicaly in time.
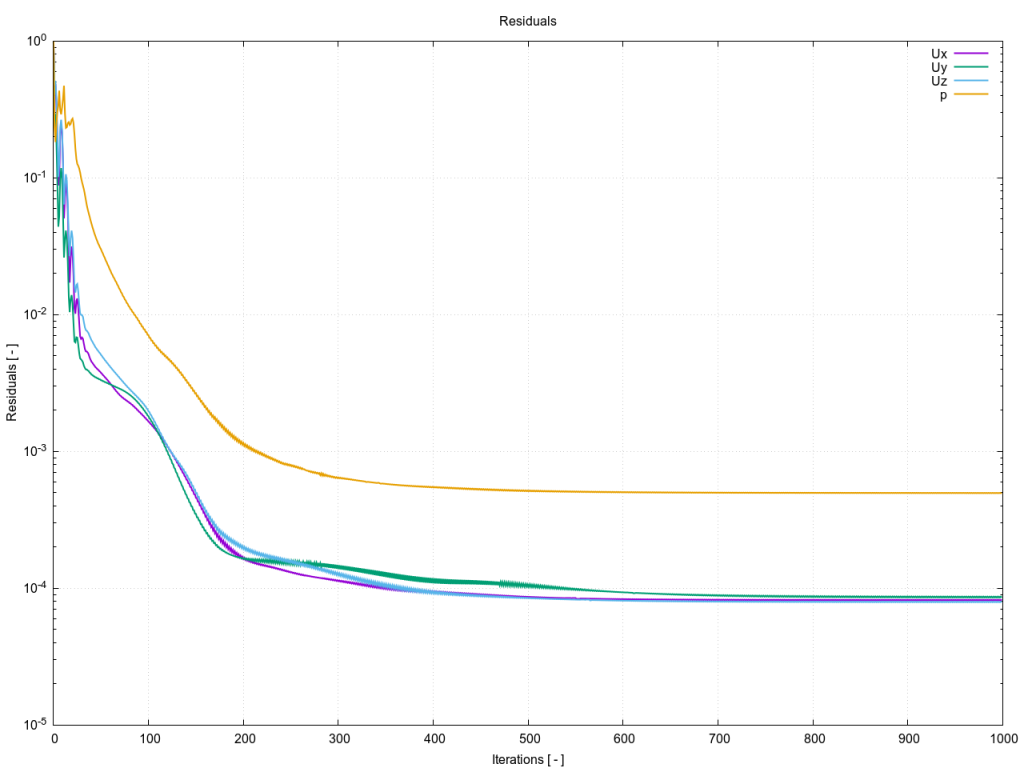
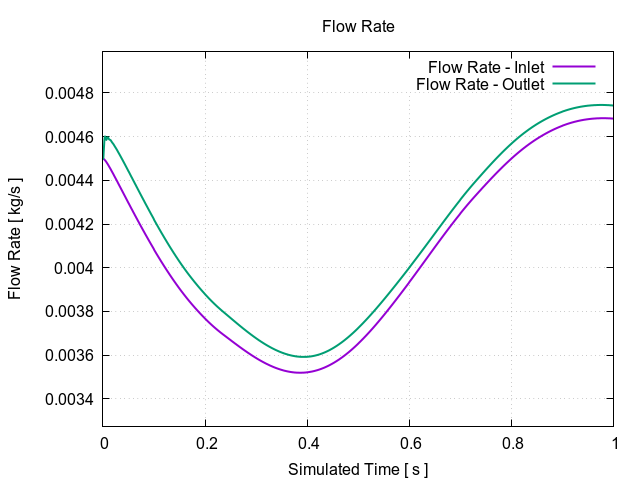
Every simulation performed in TCFD has its report in web responsive .html and pdf format: Manifold – Results Report.
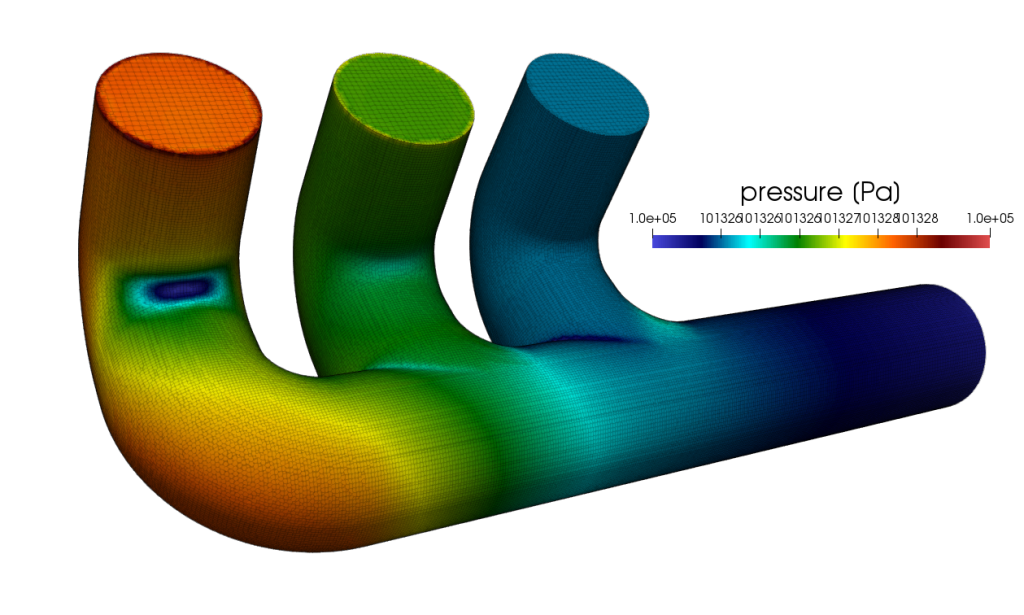
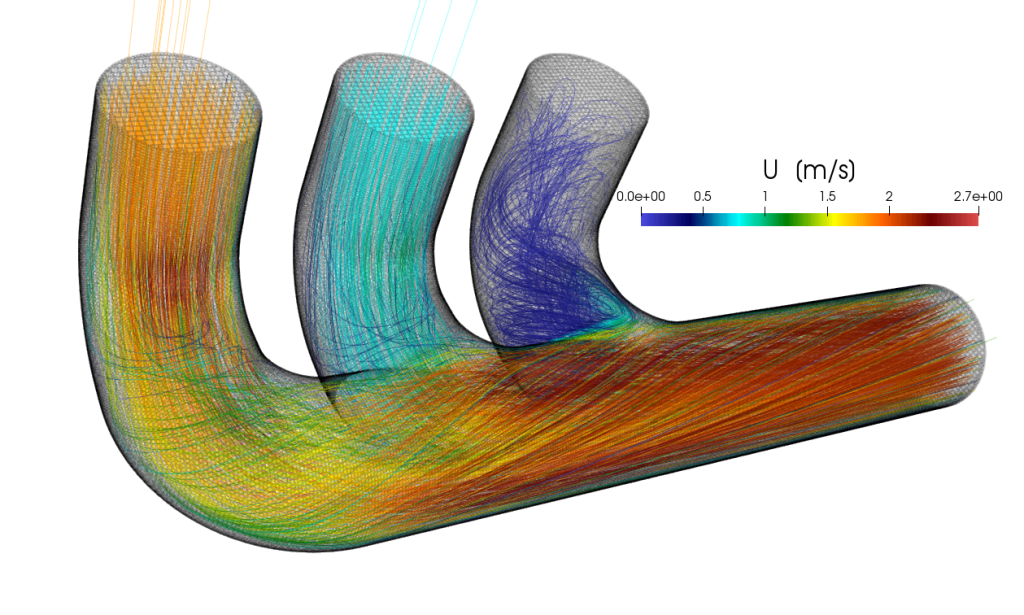
Please contact us for further information.
Download TCAE Tutorial - Exhaust Manifold
File name: manifold-multi-inlet-transient-TCAE-Tutorial-21.09.zip
File size: 9 MB
Tutorial Features: CFD, FEA, FSI, TCAE, TMESH, TCFD, TFEA, SIMULATION, FDA PUMP, RADIAL PUMP, CENTRIFUGAL PUMP, TURBOMACHINERY, INCOMPRESSIBLE FLOW, DEFORMATION, DISPLACEMENT, STRESS, MODAL ANALYSIS, INCOMPRESSIBLE, RANS, BLOOD FLOW, STEADY-STATE, AUTOMATION, WORKFLOW, RADIAL FLOW, FULL IMPELLER, SNAPPYHEXMESH, NETGEN, 3 COMPONENTS, RPM=3500, R=30mm