Previous: castellatedMeshControls Up: SnappyHexMesh mesh Next: addLayersControls
This is an automatically generated documentation by LaTeX2HTML utility. In case of any issue, please, contact us at info@cfdsupport.com.
SnapControls
This block defines parameters for snapping, i.e., process for mesh alignment with the geometry.
// Number of patch smoothing iterations before finding correspondence // to surface nSmoothPatch 3; // Maximum relative distance for points to be attracted by surface. // True distance is this factor times local maximum edge length. // Note: changed(corrected) w.r.t 17x! (17x used 2* tolerance) tolerance 2.0; // Number of mesh displacement relaxation iterations. nSolveIter 30; // Maximum number of snapping relaxation iterations. Should stop // before upon reaching a correct mesh. nRelaxIter 5; // Feature snapping // Number of feature edge snapping iterations. // Leave out altogether to disable. nFeatureSnapIter 10; // Detect (geometric only) features by sampling the surface // (default=false). implicitFeatureSnap false; // Use castellatedMeshControls::features (default = true) explicitFeatureSnap true; // Detect features between multiple surfaces // (only for explicitFeatureSnap, default = false) multiRegionFeatureSnap false;
- tolerance – relative distance for points to be attracted by surface, example of two different setups is visualized in Figure
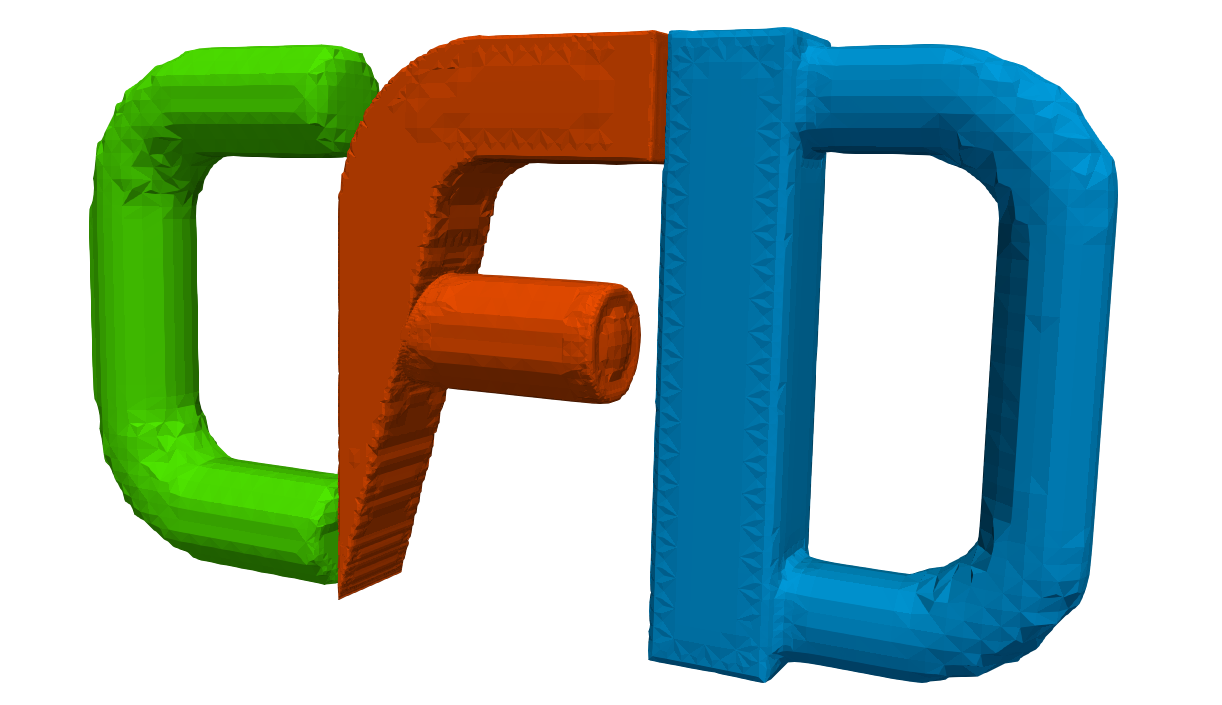
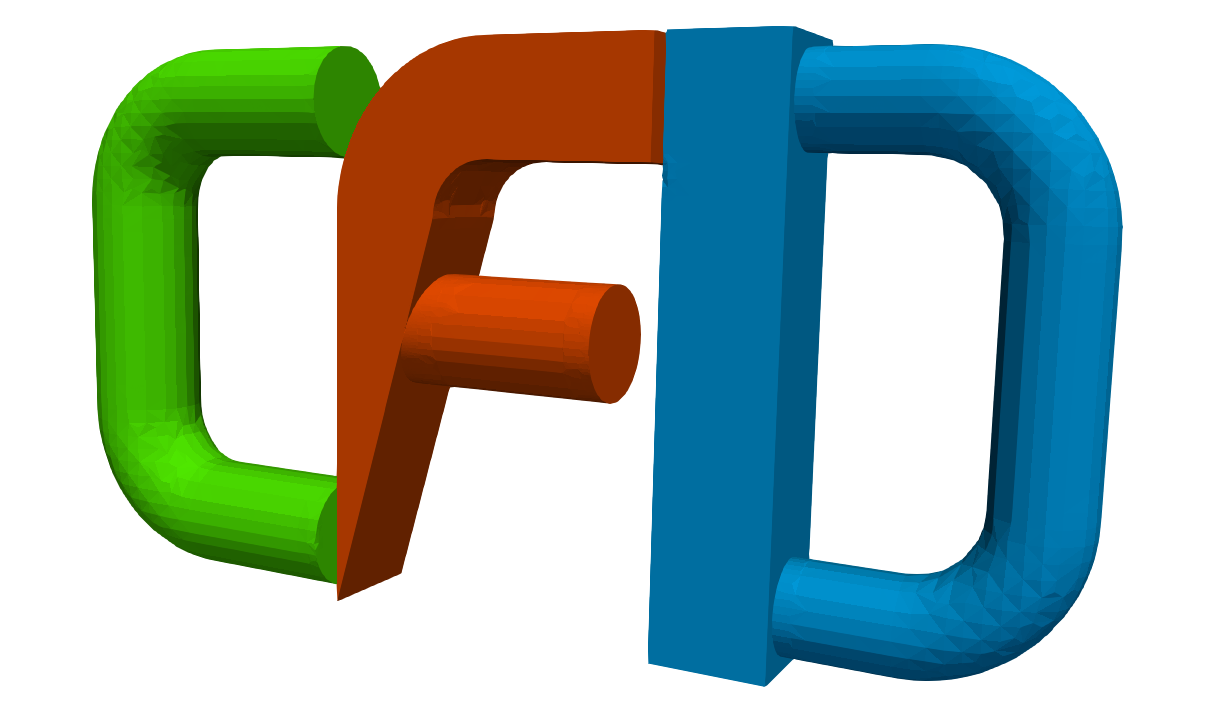
Figure: tolerance: 0.1 vs 2.0; objects surface visualization.
- implicitFeatureSnap – snaps to automatically detected feature edges following the resolveFeatureAngle parameter
- explicitFeatureSnap – snaps to manually generated feature edges, reads the features block
- multiRegionFeatureSnap – snaps to automatically detected boundary edges of each item in refinementSurfaces block
- Example of different setups is depicted in Figure
false-false-false
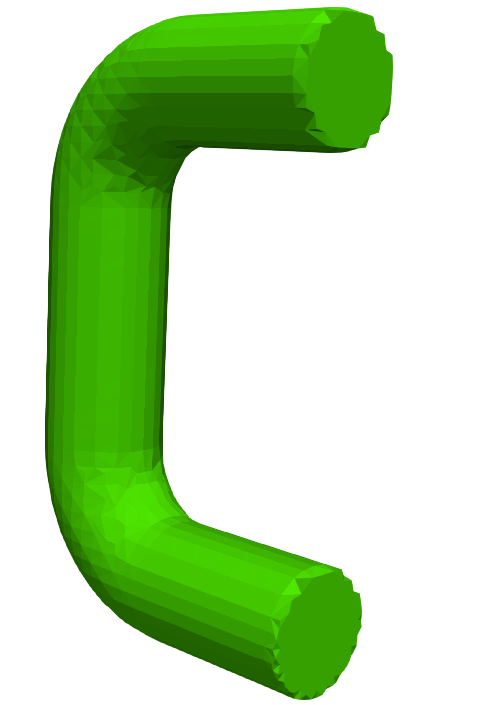
true-false-false
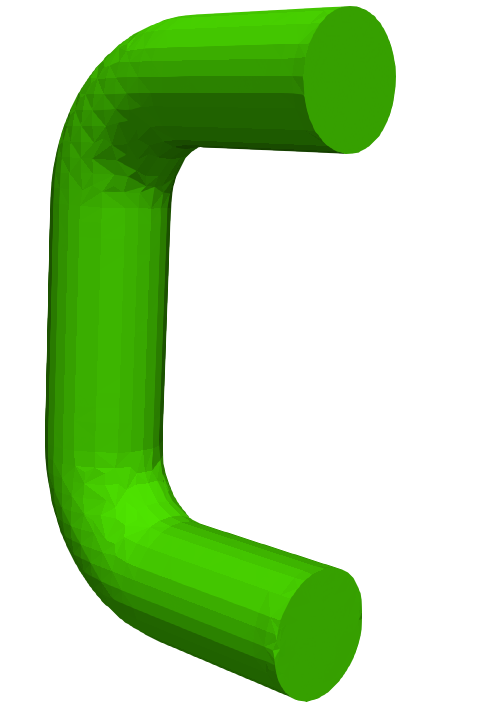
false-true-false
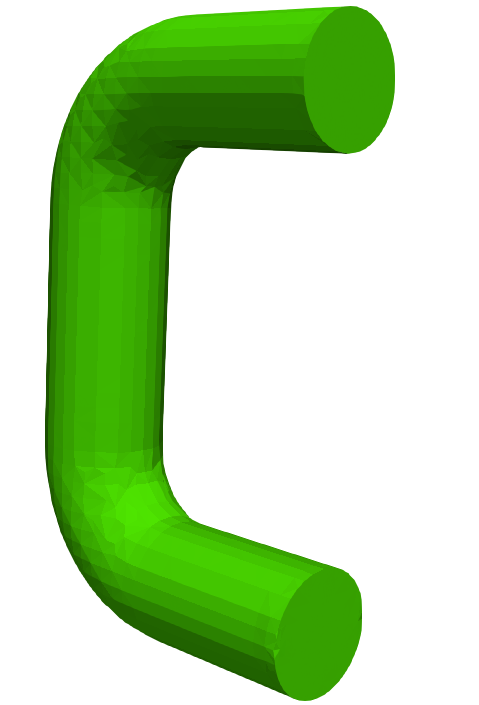
Figure: implicit*, explicit*, multiRegion* – FeatureSnap combinations.
- The multiRegionFeatureSnap make sense if your object is defined using several separte STLs.
- It is possible to split your object (one STL file) using utilities surfaceAutoPatch and surfaceSplitByPatches:
- Go to constant/triSurface directory and run following commands:
# surfaceAutoPatch C-fine.stl C-fine-split.stl 130
# surfaceSplitByPatch C-fine-split.stl - The number
is similar to includedAngle parameter in surfaceFeatureExtractDict:
– no splitting of the surface
– any triangle will be split into separate patch
- It generates three separate files which can be used for mesh generation, you can update the snappyHexMeshDict in the following way:
geometry { C-fine-split_patch0.stl { type triSurfaceMesh; name C0; } C-fine-split_patch1.stl { type triSurfaceMesh; name C1; } C-fine-split_patch2.stl { type triSurfaceMesh; name C2; } F-fine.stl { type triSurfaceMesh; name F; }
refinementSurfaces { "C-*" { level (2 2); patchInfo { type wall; } }
layers { "C[0-9]" { nSurfaceLayers 3; expansionRatio 1.5; }
- In refinementSurfaces and layers blocks it is allowed to use regular expressions.
- Now we can test different setups of multiRegionFeatureSnap, see Figure
. It clearly shows, that multiRegionFeatureSnap is enabled only when explicitFeatureSnap is enabled as well.
- Go to constant/triSurface directory and run following commands:
false-false-false
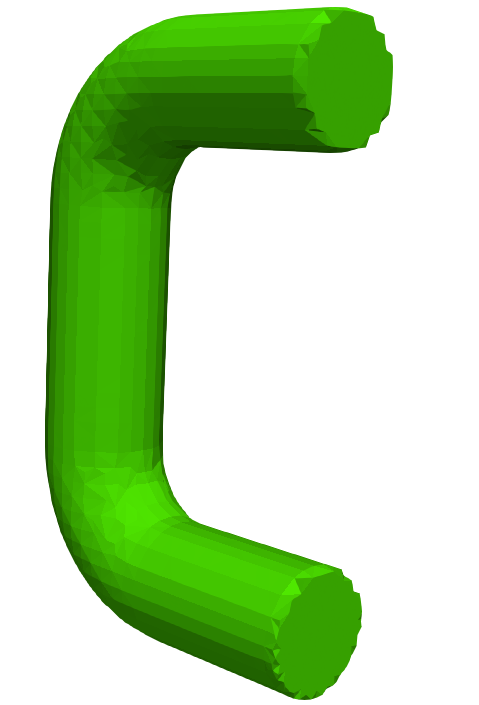
false-false-true
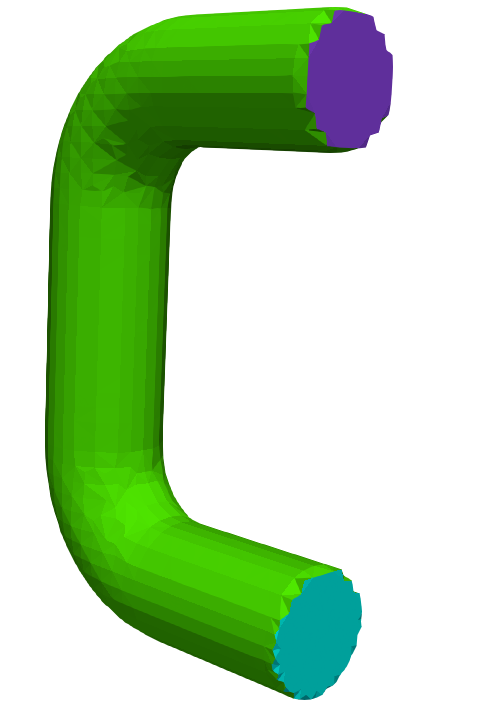
false-true-true
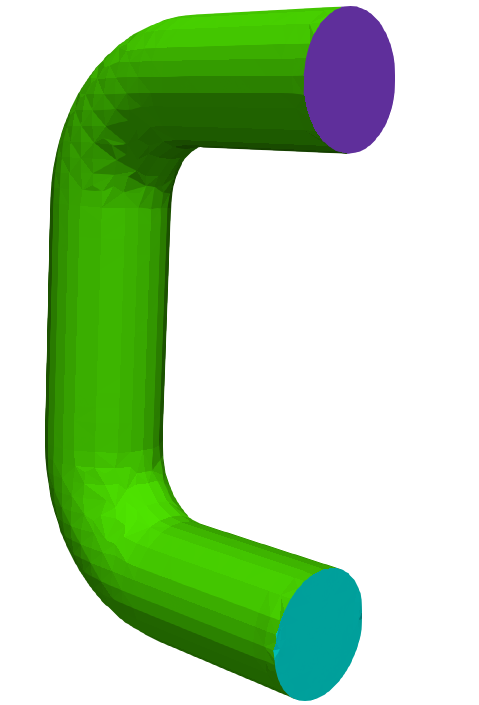
Figure: implicit*, explicit*, multiRegion* – FeatureSnap combinations.
Previous: castellatedMeshControls Up: SnappyHexMesh mesh Next: addLayersControls